When businesses need moulds that marry micrometer accuracy with relentless durability, they turn to specialists. As a leading Custom Precision Plastic & Metal Mould Manufacturing Solutions Provider, we’ve spent decades perfecting the art and science of creating moulds that perform flawlessly under pressure. Whether you’re in automotive, medical devices, or consumer electronics, our mission is simple: deliver moulds that accelerate your production while slashing downtime and waste.
Why Partner with Us? The Unbeatable Edge
1. Cutting-Edge Technology & Master Craftsmanship
- Our workshops run CNC machining centers and EDM (Electrical Discharge Machining) equipment capable of holding tolerances within ±0.005mm .
- Unlike shops that just automate, we pair tech with human expertise. Our engineers hand-polish cavities to mirror finishes and tweak texturing for surfaces from matte to wood-grain—ensuring your final product looks and functions perfectly .
-
Real impact: One medical client reduced injection cycle times by 22% after switching to our high-conductivity steel moulds with optimized cooling channels.
2. Military-Grade Quality Control
- Every mould undergoes 3-stage inspection: raw material certification (traceable to mill sources), in-process CMM (Coordinate Measuring Machine) checks, and final trial runs with sample parts measured against your CAD specs .
- We’re ISO 9001:2015 certified, but go further with industry-specific validations like IATF 16949 for automotive tooling. No "close enough" here—just data-driven perfection .
3. From Prototype to Million-Unit Runs
- Need 500 prototype housings next week? Our rapid tooling division uses aluminum moulds for 72-hour turnarounds.
- Scaling to high-volume production? Hardened steel moulds handle 1M+ cycles without wear. We design for longevity—incorporating self-lubricating guides and corrosion-resistant alloys like AISI 1.2316 steel for PVC or abrasive composites .
4. Solutions, Not Just Moulds
-
End-to-end service includes DFM (Design for Manufacturability) analysis to catch costly errors early. Example: We reconfigured a client’s electronics enclosure mould, eliminating undercuts and cutting their assembly labor by 40%.
-
After-sales care covers everything from emergency polishing to lifetime maintenance plans. One client’s 8-year-old production mould still runs like new thanks to our scheduled upkeep.
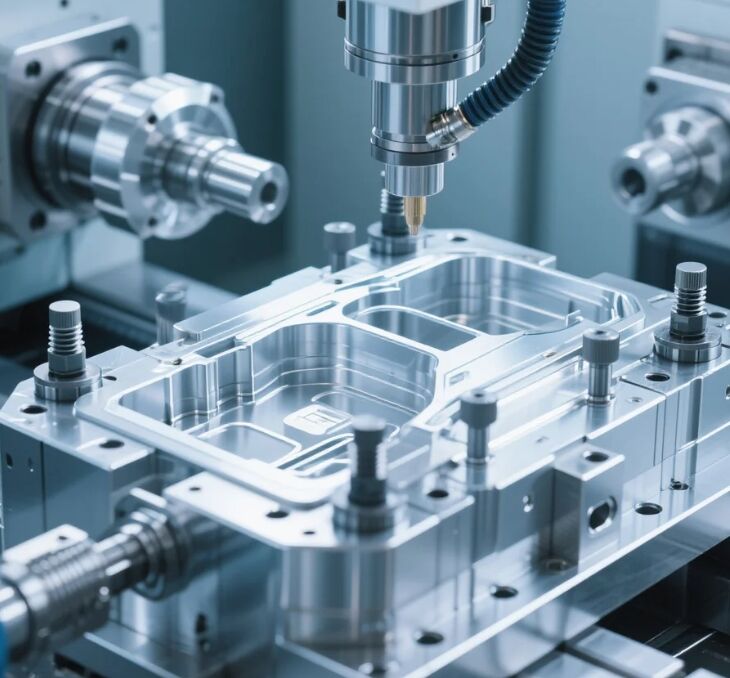
Industries We Empower
-
Medical: USP Class VI-compliant moulds for IV connectors, surgical tools.
-
Automotive: Core inserts for dashboard panels, fog lamp housings with zero sink marks.
-
Consumer Tech: Overmoulds for wearables, ultra-high-gloss TV bezels.
Our Partners’ Success Stories
"After two mould failures from other vendors, these experts delivered a multi-cavity tool for PET preforms. We’ve run 16M units with ±0.02mm consistency. Their 24/7 technical support saved a $250K production line halt."
— Operations Director, Beverage Packaging Firm
Ready to Elevate Your Manufacturing?
Precision isn’t just our specialty—it’s our obsession. With capabilities spanning micro-moulding for 0.1g medical parts to 20-tonne multi-slide tools, we’re equipped to turn your vision into production-ready reality.
Let’s discuss your project:[email protected]
Explore our full case studies and technical specs at [https://www.7-swords.com/]